Let’s break this down into a simple cause and effect. Less capacity = fewer trucks to move shipping supplies = tighter schedules & increased costs. Of course that would then mean the opposite would also be true. More capacity = more trucks to move shipping supplies = flexible schedules = lower costs. But, what causes this rise and fall? Well, several factors are involved that go far beyond the number of trucks on the road or ones sitting in the lots of trucking companies.
A few of these factors are as follows.
Weather Conditions
Extreme weather conditions can quickly shut down roads for long periods of time. For instance, snowstorms in the Midwest and Northeast during the wintertime, rain and tropical storms in the southern regions during hurricane season, both of these can play apart in trucking industry. These weather conditions not only will affect the region their in, but the entire nation because the trucks cannot travel from the regions being affected by the weather. Which delays the delivery of shipping supplies; truck capacity decreases, and then shipping costs increase.
Seasonal Variations
During busy shipping seasons truck capacity will also decrease, which causes shipping costs to potentially increase. A few peak shipping seasons are harvest time, which is spring through mid summer, when the trucks are hauling huge amounts of fresh produce. Also, during August through October when back-to-school supplies are in high demand, as well as holiday items.
Truck Driver Shortage
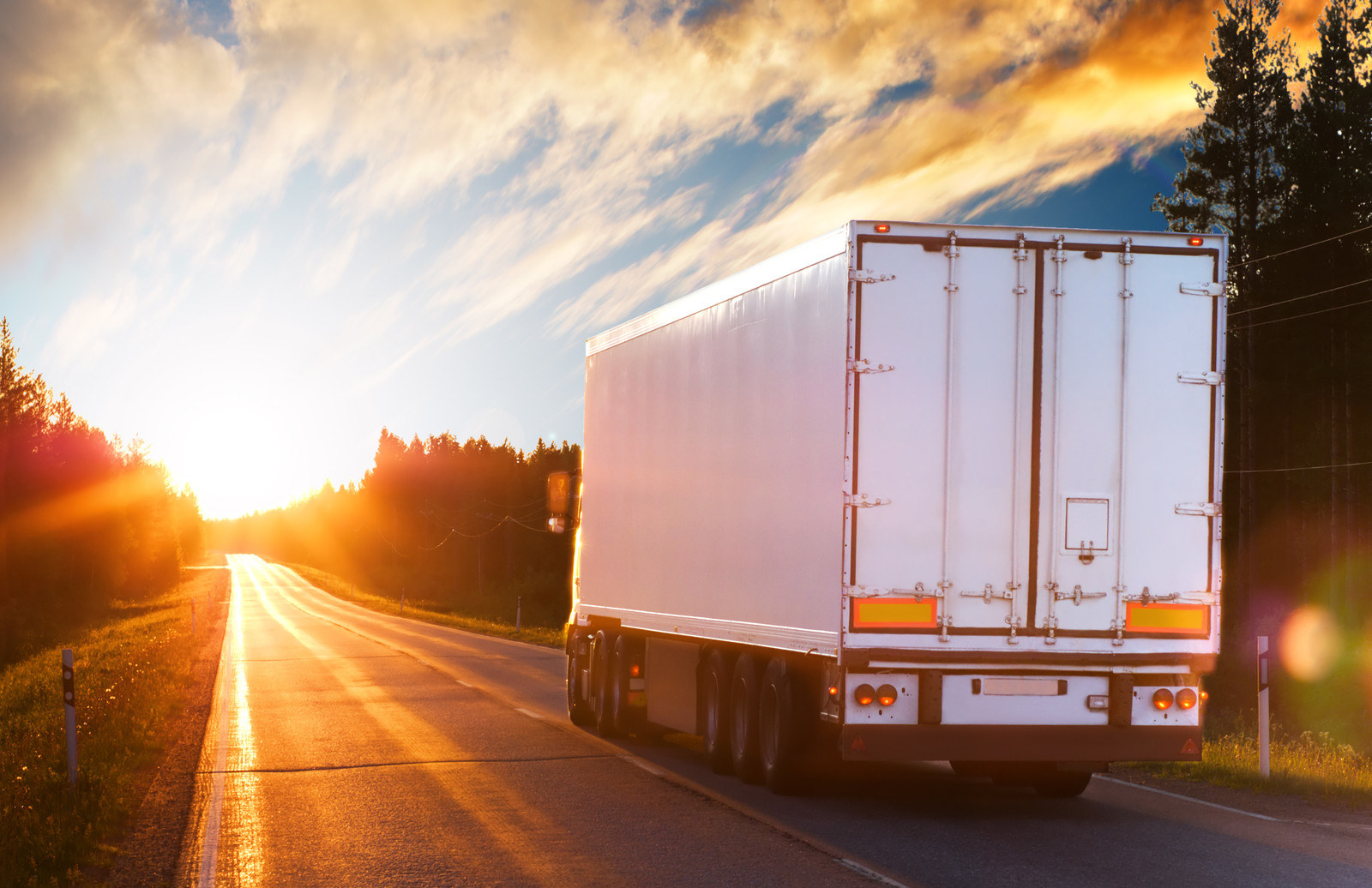
Increased Regulations
This factor is a big one. Because the government, both state and federal, is stepping in and dictating certain aspects of the trucking industry, it’s affecting productivity, which in turn affects capacity, which affects costs. A few of these regulations include:
* Hours of Service (HOS) Meaning that these rules dictate the maximum number of hours that a driver can be on the road during a long haul. This also includes a reset requirement.
* California Air Resources Board Meaning that every truck operating in California is subject to strict emissions standards. In order to meet this requirement, newer and more costly vehicles need to be purchased. Which then of course drives up shipping costs.
* Electronic Logging Devices (ELD) Starting at the beginning of December 2017 ELDs will replace paper logs for recording hours of service. While it’s not 100% known how this will play out, the expected cost of the ELDs will reduce the ability to deploy these in all a shippers trucks, further reducing trucking capacity.
Escalating Costs
The costs in the trucking industry are consistently rising. The cost to maintain or repair vehicles, gas, while it fluctuates, slowly continues to rise over time, and labor costs. All of these play a factor in the cost of shipping supplies.
So, while trucking capacity doesn’t seem all that exciting on the surface. Once you start pulling back the layers and realizing its effect on the industry as a whole, you realize how vital understanding it can be for you and your business.